Coating Service
I. ANTI-COROSSION COATING SERVICE
1. FUSION BONDED EPOXY COATING (FBE)
Fusion Bonded Epoxy (FBE) is an excellent anti-corrosion coating for oil and gas pipelines because its strong adhesion to steel brings about superior long term corrosion resistance and protection of pipelines operating smoothly at required temperatures during their designed life.
Also, the excellent resistance to corrosion of FBE coating helps to reduce the total cost of cathodic protection during the operation of the pipeline.
Capability/Property
|
FBE
|
Minimum Pipe Diameter ………………………………………………………
|
60.3 mm (2”)
|
Maximum Pipe Diameter ………………………………………………………
|
1219.2 mm(48”)
|
Minimum Pipe Length …………………………………………………………
|
9.5 m
|
Maximum Pipe Length ………………………………………………………...
|
12.7 m
|
Maximum Recommended Operating Temperature ……………………………
|
140 °C (284oF)
|
.jpg)
2. THREE LAYER POLYETHYLENE COATING (3LPE)
Three layer polyethylene coating (3LPE) is a multilayer coating composed of three functional components: a FBE primer, a copolymer adhesive and an outer layer of high density polyethylene to provide excellent corrosion protection and mechanical protection for oil & gas pipelines at operating temperature up to 85oC.
The 3LPE System achieves superior long term corrosion resistance and excellent mechanical protection for small and large diameter pipelines operating at high temperature thanks to strong adhesion of FBE to steel and the tough outer layer of high density polyethylene. The 3LPE system can be applied in a wide range of thicknesses to meet project specifications and requirements.
Capability/Property
|
3LPE
|
|
Minimum Pipe Diameter ……………………………………………………….
|
60.3 mm (2”)
|
Maximum Pipe Diameter ………………………………………………………
|
1219.2 mm (48”)
|
Minimum Pipe Length …………………………………………………………
|
9.5 m
|
Maximum Pipe Length ………………………………………………………...
|
12.7 m
|
Minimum/Maximum Recommended Operating Temperature (Onshore) …….
|
-20°C to 65°C(-4°F to 149°F)
|
Minimum/Maximum Recommended Operating Temperature (Offshore) …….
|
-20°C to 85°C(-4°F to 185°F)
|
.jpg)
3. THREE LAYER POLYPROPYLENE COATING (3LPP)
Three layer polypropylene coating (3LPP) is a multilayer coating composed of three functional components: a FBE primer, a copolymer adhesive and an outer layer of polypropylene to provide excellent corrosion protection and mechanical protection for oil & gas pipelines at operating temperature up to 140oC.
The 3LPP System achieves superior long term corrosion resistance and excellent mechanical protection for small and large diameter pipelines operating at high temperature thanks to strong adhesion of FBE to steel and the tough outer layer of polypropylene. The 3LPP system can be applied in a wide range of thicknesses to meet project specifications and requirements.
Capability/Property
|
3LPP
|
Minimum Pipe Diameter …………………………………………………
|
88.9 mm (3”)
|
Maximum Pipe Diameter …………………………………………………
|
1219.2 mm (48”)
|
Minimum Pipe Length …………………………………………………...
|
9.5 m
|
Maximum Pipe Length …………………………………………………...
|
12.7 m
|
Minimum/Maximum Recommended Operating Temperature (Onshore) …..
|
-20°C to 110°C (-4°F to 230°F)
|
Minimum/Maximum Recommended Operating Temperature (Offshore) …..
|
-20°C to 140°C (-4°F to 284°F)
|
.jpg)
II. CONCRETE WEIGHT COATING SERVICE
This concrete weight coating system provides negative buoyancy and mechanical protection for offshore pipelines.Concrete weight coating uses impingement application process making it suitable for both small and large diameter pipelines.
This coating method is available in various thicknesses and densities to provide the appropriate level of buoyancy control and meet project technical specifications. Available thicknesses are up to 150 mm (6”), which achieves a high level of mechanical protection and stability.
It can be applied over all anti-corrosion coatings and insulation coatings without harm to the long term corrosion protection and thermal insulation of the pipelines.
Capability/Property
|
Concrete Weight Coating
|
Characteristic Proctor Cylinder Compressive Strength (28 days) ……….
|
30-40 MPa (4350-5800 psi)
|
Characteristic Cube Compressive Strength (28 days) …………………...
|
40-50 MPa (5800-7250 psi)
|
Minimum Pipe Thickness ………………………………………………..
|
40 mm
|
Maximum Pipe Thickness ……………………………………………….
|
150 mm
|
Minimum Pipe Diameter …………………………………………………
|
168.3 mm (6”)
|
Maximum Pipe Diameter ………………………………………………...
|
1219.2 mm (48”)
|
Minimum Pipe Length …………………………………………………...
|
9.5 m
|
Maximum Pipe Length …………………………………………………..
|
12.7 m
|
.jpg)
III. INSULATION COATING SERVICE
1. POLYURETHANE FOAM (PUF) THERMAL INSULATION COATING
PUF thermal insulation coating designed for offshore flow assurance is critical to the oil and gas industry to reduce heat loss and prevent hydrate formation for oil pipelines and helps to maintain viscosity in hot oil pipelines.
The coating system is a polyurethane-based insulation coating composed of three functional components: a FBE primer, a layer of polyurethane foam and an outer layer of high density polyethylene/polypropylene to provide excellent corrosion protection, superior insulation and mechanical protection for oil pipelines at operating temperatures up to 150oC.
Capability/Property
|
PU Foam
|
Minimum Pipe Diameter ……………………………………………...
|
100 mm (4”)
|
Maximum Pipe Diameter ……………………………………………..
|
600 mm (24”)
|
Minimum Operating Temperature ……………………………………
|
-20°C (-4°F)
|
Maximum Operating Temperature ……………………………………
|
140°C (284°F)
|
Minimum Pipe Length ………………………………………………...
|
9.5 m
|
Maximum Pipe Length ………………………………………………..
|
12.7 m
|
OHTC (“U” Value) ……………………………………………………
|
<2.0 W/m2.K (0.352 BTU/hr.ft2.F)
|
Maximum Water Depth ……………………………………………….
|
300 m
|
K-Value ………………………………………………………………..
|
<0.042 W/m.K
|
.jpg)
2. MULTILAYER POLYPROPYLENE (MLPP) INSULATION COATING
Multilayer Polypropylene (MLPP) Insulation Coating is a technologically advanced coating system for offshore flow assurance. MLPP Insulation Coating can be designed and manufactured to provide excellent insulation in subsea pipelines with operating temperatures up to 150°C (302°F) and depths of up to 3000 m (9842’).
In MLPP thermal insulation coating, 3LPP coated pipe is conveyed through infrared heating system for outer layer fusion and improving adhesion between preceding and successive layers. Hot PP Foam is extruded onto the heated 3LPP coated pipe. Then the pipe is cooled down by quenching system. This step will be repeated as many times as necessary to achieve the desired thermal insulation requirements. Following the final polypropylene foam coating application, a final single layer of UV stabilized polypropylene topcoat is applied by extrusion process over the polypropylene foam.
Capability/Property
|
MLPP
|
Minimum Pipe Diameter ………………………………………......
|
100 mm (4”)
|
Maximum Pipe Diameter ……………………………………….....
|
600 mm (24”)
|
Minimum Operating Temperature …………………………………
|
-35°C (-31°F)
|
Maximum Operating Temperature ………………………………...
|
150°C (302°F)
|
Minimum Pipe Length ……………………………………………..
|
9.5 m
|
Maximum Pipe Length …………………………………………….
|
12.7 m
|
OHTC (“U”Value) …………………………………………………
|
<1.5W/m2.K(0.264 BTU/hr.ft2.F)
|
Maximum Water Depth ……………………………………………
|
3000 m
|
.jpg)
IV. BENDS & FITTINGS COATING SERVICE
1. Bend and Fitting for 2/3LPE – 2/3LPP Anti-corrosion coating
We can apply 2/3LPE, 2/3LPP anti-corrosion coating systems designed for subsea production structures. These systems can be coated for bends and fittings. They can be applied in a wide range of thicknesses to meet project requirements for both shallow and deep water applications.
This coating provides excellent long-term anti-corrosion protection for bends in subsea environments and in harsh environments with temperatures up to 140°C (285°F). The two and three-layer polyethylene and polypropylene coating systems are suitable for all the existing anti-corrosion.
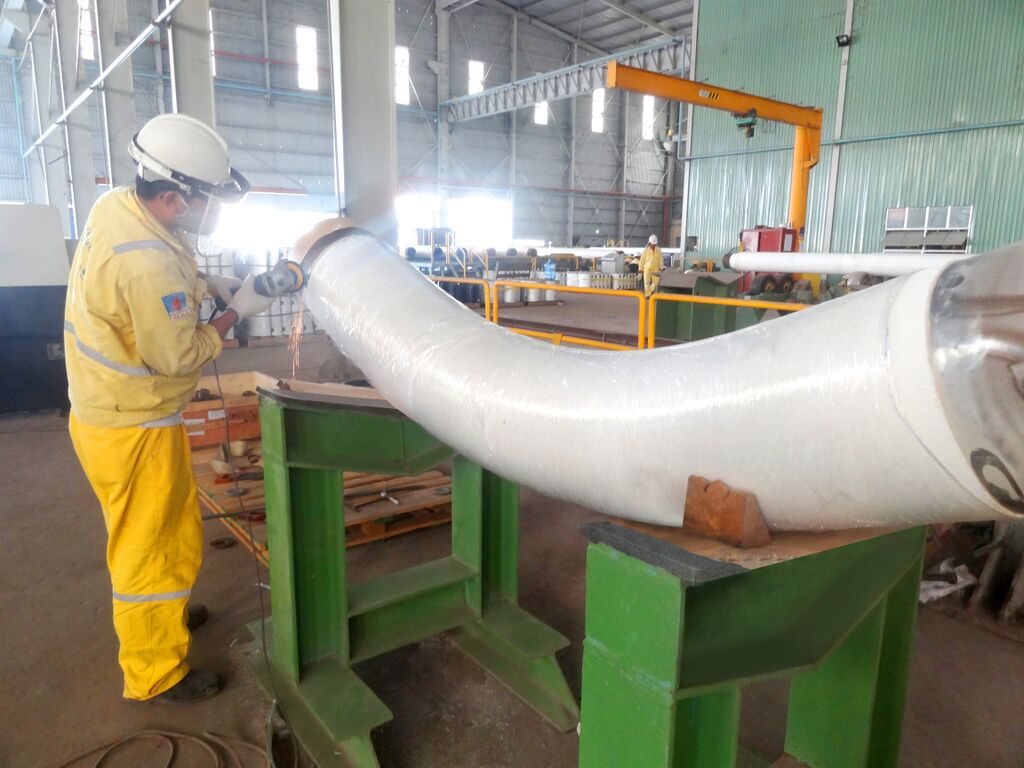
2. Bend & Fittings for SPU - Insulation coating
They can be applied in a wide range of thicknesses and configurations to meet technical performance designs based on the specific requirements for both shallow and deep water applications.
This coating provides superior thermal insulation properties. The adhesion properties of the primer or the FBE result in corrosion protection and resistance to cathodic disbondment.
It can be used for thermally insulating fabricated custom parts of subsea production systems for bends. The SPU systems can be applied for technical performance designs based on the specific requirements of each project
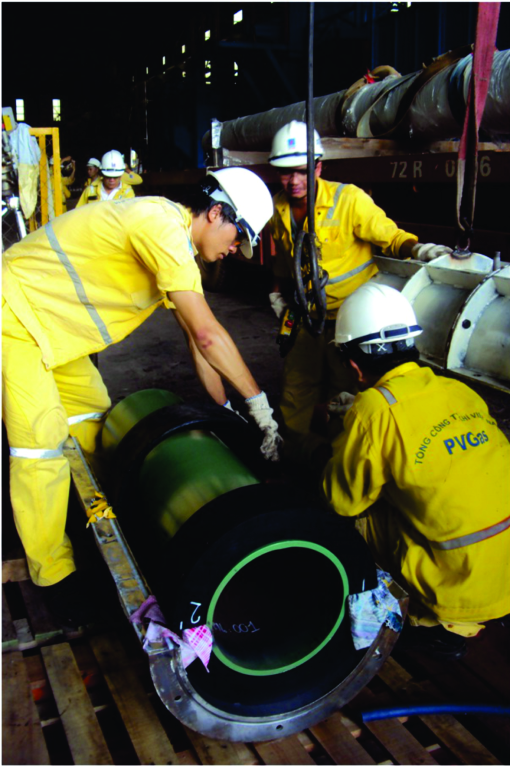
V. FIELD JOINT COATING SERVICE
1. Field joint coating for anti-corrosion 3LPE and 3LPP coated pipelines:
Heat Shrink Sleeve 3LPE and Heat Shrink Sleeve 3LPP coating technologies are used and comprised of the same PE and PP material grades as the mainline (factory-applied) coating to provide equivalent performance and deliver truly consistent end-to-end pipeline coating performance.
2. Field joint coating for insulation coated pipelines:
Polyurethane Foam (PU Foam) and Solid Polyurethane (SPU) coating technologies are used and comprised of the same PU Foam and SPU material grades as the mainline (factory-applied) coating to provide equivalent performance and deliver truly consistent end-to-end pipeline coating performance.
.jpg)
IV. TESTING SERVICES
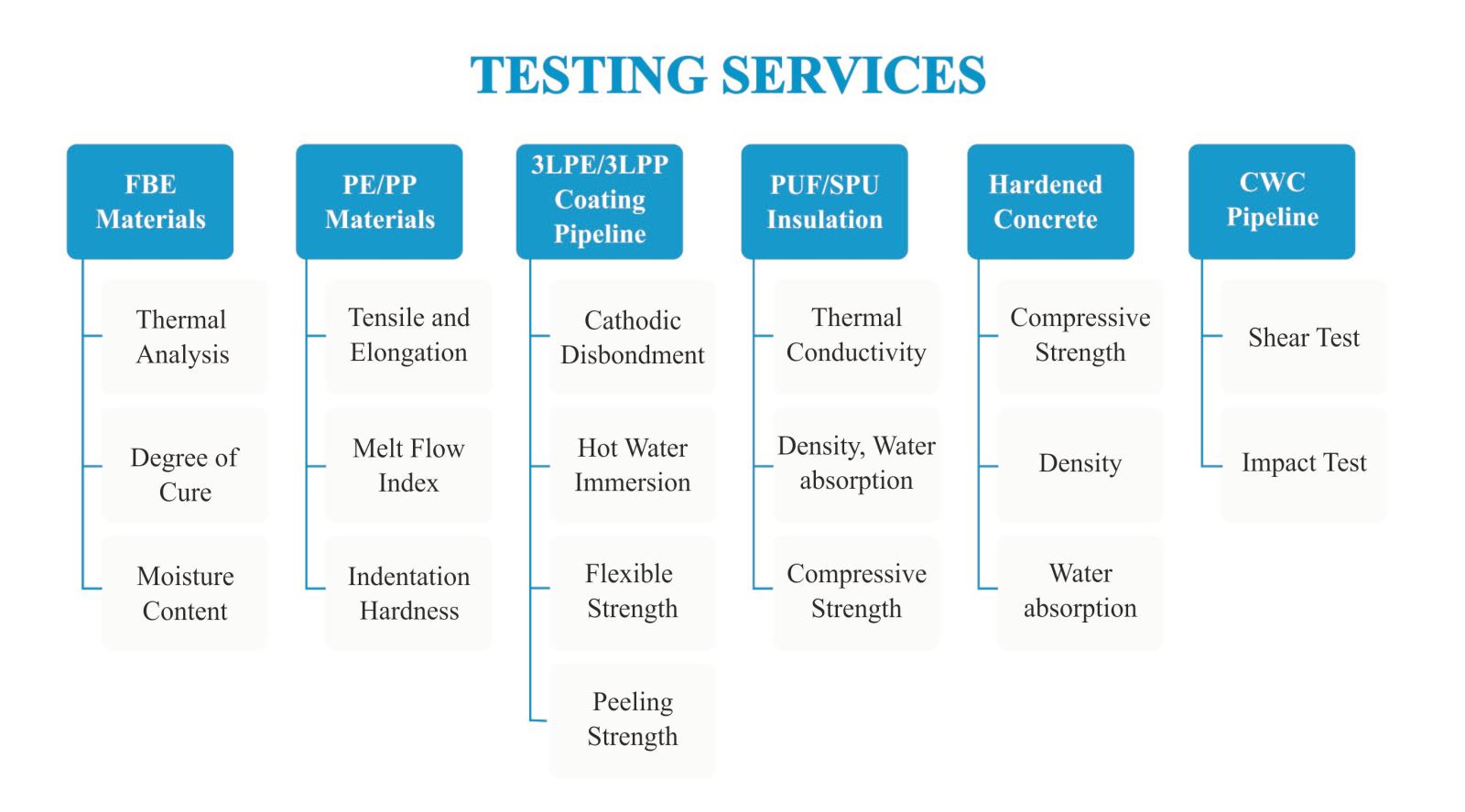
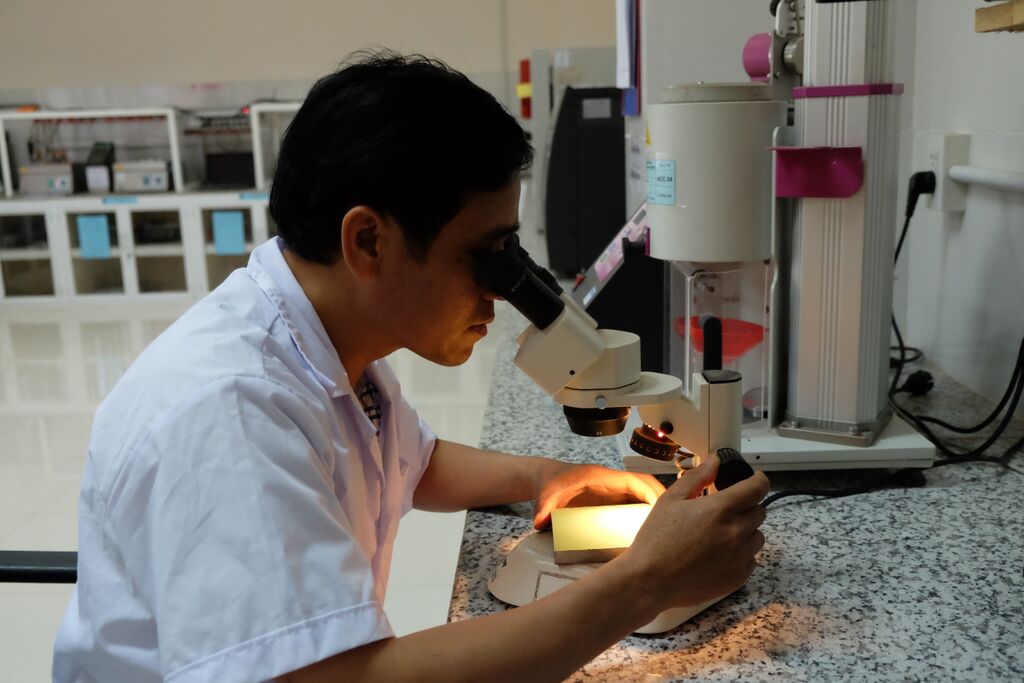