PetroVietnam Gas Vung Tau Processing Company - A 100%-owned company of PetroVietnam Gas Joint Stock Corporation is awarded The Government’s Emulation Flag 2012
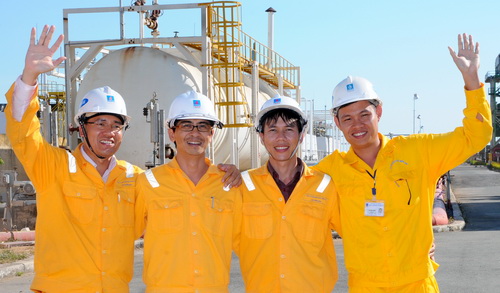
After 15 years since the first gas flow was brought onshore, Gas Processing Company with PetroVietnam Gas Joint Stock Corporation has processed and supplied over 19.5 billion m3 of dry gas, more than 4 million tons of LPG and 1.38 million tons of Condensate; providing fuels and feedstock for production of approximately 10% national power output, 30% fertilizer output, 10% gasoline output and meeting 30% LPG demand for industrial and household consumption of the country.
With active contributions and achievements to the socio-economic development, PV Gas Vung Tau Processing Company was honored to receive the noble prize - Emulation flag for Outstanding Achievement in 2012 according to the Prime Minister’s decision, becoming the only company of PV Gas awarded with this title during the year.
PV Gas Vung Tau Processing Company (Initialed as KVT), the leading company of PetroVietnam Gas Joint Stock Corporation (PV Gas) has its main functions and tasks including: management, operation of gas projects; processing of dry gas, Liquefied Petroleum Gas and Condensate.
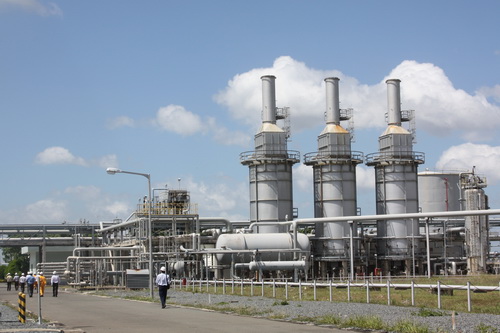
In 2012, in spite of many difficulties in production situation such as: wet gas output provided onshore by the field owners becoming unstable, affecting the efficiency in liquid product recovery... but the Company leadership has actively proposed solutions to maintain continuous production activities, maximizing the efficiency of product recovery, contributing to over-fulfillment of PV Gas annual plan. The Company has reached the target ahead of schedule and exceeded the targeted norms for LPG, condensate, service revenues of the 2012 plan, increased over those completed in 2011 with good quality. Details are as follows:
- LPG output reached the target ahead of schedule by 59 days; completed 100% of the plan on 02/11/2012 and until 31/12/2012 produced and supplied 253.4 thousand tons (representing 119% of the plan), increased by 6% over 2011 (2001: 240 thousand tons);
- Condensate output reached the target by the time of 54 days; completed 100% of the plan at the end of 07/11/2012, and until 31/12/2012 produced and supplied 58.4 thousand tons (representing 117% of the plan), increased by 3% over 2011 (2011: 56.8 thousand tons);
- Condensate output reached the target by the time of 54 days; completed 100% of the plan at the end of 07/11/2012, and until 31/12/2012 produced and supplied 58.4 thousand tons (representing 117% of the plan), increased by 3% over 2011 (2011: 56.8 thousand tons);
- Product quality always meet the norms committed by PetroVietnam Gas Joint Stock Corporation, winning customer confidence; and there are no complaints about the product quality of the Plant. LPG product was awarded with the certificate of ASTM D 1835 conformity issued by QUATEST 3. The inspection team from STAMEQ in 2012 highly rated activities of quality and quantity control implemented by the Company.
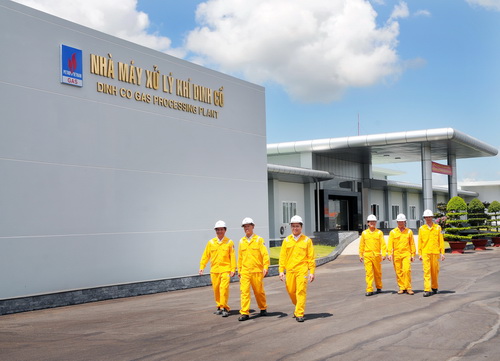
In order to achieve above results, throughout its operation, KVT has built and maintained the Safety - Health - Environment culture to "Prevent damages to Human, Property and Environment” and “Aiming at satisfying the growing customer demand for Clean, Quality and Competitive Fuel". Therefore, despite management and operation of very complicated gas facilities with potential fire risks, in over 15 years of operation, the Company has always ensured safe and efficient operation of gas facilities and was highly rated by fire protection and environment organizations with respect to Safety - Quality – Environment activities. International safety assessment teams (from Germany, BP, LOYD'S and Norway) highly evaluated the safety, health and environment activities in the Company. The Company’s products and services are always of good quality, with no quality complaint reflected by customers.
Besides, in the course of business activities, KVT has always made innovations in all areas in order to improve productivity, quality, work efficiency, saving cost and time. In 2012, the total saving cost from management and production innovations reached 164 billion 496 million VND, including: benefiting due to optimization of the system product output, shortening the maintenance downtime yielded 127 billion 640 million VND (especially, the reduced downtime of 125 hours for Dinh Co Gas Processing Plant maintenance and early resumption of normal operation have helped save approximately 38 billion VND); saving thanks to movements of innovation initiatives, production rationalization was 32 billion VND; saving from management activities (bidding, construction and material, fuel/feedstock, etc...) was approximately 5 billion VND.
Besides, in the course of business activities, KVT has always made innovations in all areas in order to improve productivity, quality, work efficiency, saving cost and time. In 2012, the total saving cost from management and production innovations reached 164 billion 496 million VND, including: benefiting due to optimization of the system product output, shortening the maintenance downtime yielded 127 billion 640 million VND (especially, the reduced downtime of 125 hours for Dinh Co Gas Processing Plant maintenance and early resumption of normal operation have helped save approximately 38 billion VND); saving thanks to movements of innovation initiatives, production rationalization was 32 billion VND; saving from management activities (bidding, construction and material, fuel/feedstock, etc...) was approximately 5 billion VND.
Besides, in the course of business activities, KVT has always made innovations in all areas in order to improve productivity, quality, work efficiency, saving cost and time. In 2012, the total saving cost from management and production innovations reached 164 billion 496 million VND, including: benefiting due to optimization of the system product output, shortening the maintenance downtime yielded 127 billion 640 million VND (especially, the reduced downtime of 125 hours for Dinh Co Gas Processing Plant maintenance and early resumption of normal operation have helped save approximately 38 billion VND); saving thanks to movements of innovation initiatives, production rationalization was 32 billion VND; saving from management activities (bidding, construction and material, fuel/feedstock, etc...) was approximately 5 billion VND.
By Kieu Yen